Applications Applications Applications Applications
- Home
- /
- Applications
- /
- Polymer Synthesis
Polymer Synthesis
Catalysts for Polyethylene Terephthalate (PET)Synthesis
Polyethylene Terephthalate (PET) is one of the world’s most widely produced thermoplastic polyesters, used in applications ranging from beverage bottles and food containers to textile fibers and engineering resins. In the production of PET, the choice of catalyst plays a critical role in determining the efficiency of the polymerization process and the final product’s physical and mechanical properties.
Dorf Ketal‘s ACtivate™ and Tyzor® titanate catalysts offer significant advantages over traditional metal-based catalysts such as antimony trioxide or manganese acetate. These organotitanium compounds act as highly effective esterification and polycondensation catalysts, enabling manufacturers to achieve high molecular weight PET with lower color formation, faster reaction rates, and improved downstream processability.
In the melt phase of PET production, ACtivate™ and Tyzor® catalysts promote the transesterification of dimethyl terephthalate (DMT) or the direct esterification of terephthalic acid (PTA) with ethylene glycol (EG). This reaction forms oligomers that are subsequently polycondensed into high-molecular-weight PET. The use of ACtivate™ and Tyzor® catalysts enables efficient conversion with reduced side reactions, such as olefin formation, which can lead to color bodies or undesirable byproducts.
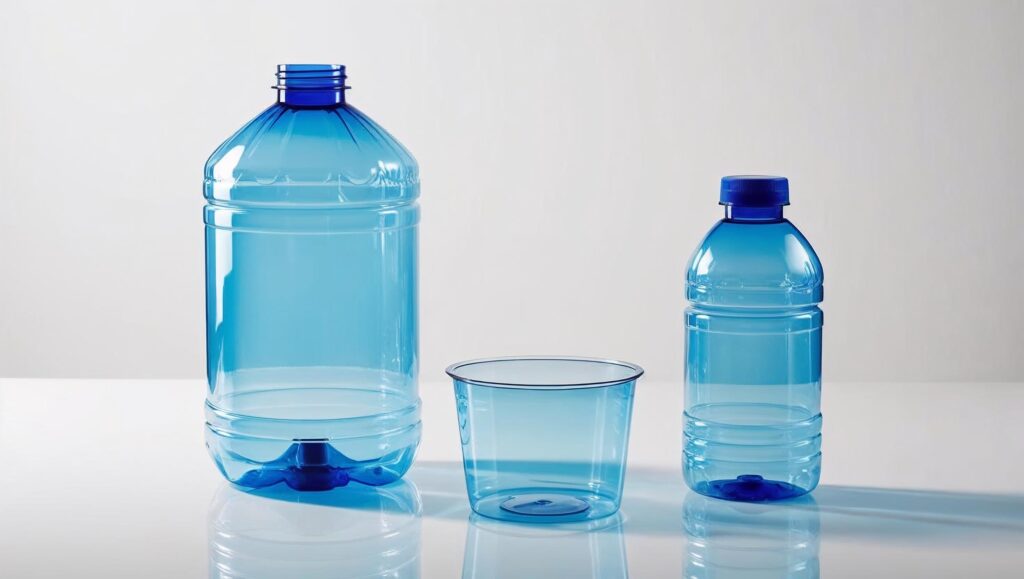
ACtivate™ and Tyzor® Solutions
Efficient Esterification Process
Efficient Esterification Process
Low-Color PET for Packaging
Low-Color PET for Packaging
Improved Blow Molding Performance
Improved Blow Molding Performance
Food-Safe Metal-Free Catalysis
Food-Safe and Heavy Metal-Free Catalysis
Reduced Acetaldehyde Formation
Reduced Acetaldehyde Formation
Enhanced Fiber Properties in Textile PET
Enhanced Fiber Properties in Textile PET
Smart Reactivity for PET Synthesis
Smart Reactivity for PET Synthesis
Additionally, titanate catalysts offer a low environmental footprint, with no residual heavy metals in the polymer chain. This is increasingly important for brands and manufacturers seeking food-contact compliance and alignment with global sustainability directives. Dorf Ketal's Activate™ and Tyzor® catalysts have been shown to eliminate the need for certain co-monomers (e.g., isophthalic acid) and reduce acetaldehyde levels in PET resins, simplifying formulation and improving product safety.
The ability to maintain high tensile strength and reduced brittleness in PET fibers is another performance metric where Activate™ and Tyzor® excels. In fiber-grade PET, the catalyst system directly impacts fiber uniformity, dyeability, and spinnability. Dorf Ketal's solutions are engineered to maintain strength and elongation characteristics while minimizing polymer degradation during spinning and drawing.
With ongoing global shifts toward recyclable and food-safe polymers, Activate™ and Tyzor® catalysts position PET manufacturers to lead in performance, process optimization, and environmental stewardship.
Polyolefins Synthesis
Polyolefins—including polyethylene (PE) and polypropylene (PP)—represent the largest volume class of polymers used globally, with applications spanning packaging, automotive parts, medical devices, and infrastructure materials. The production of these polymers relies heavily on advanced catalyst systems, and Dorf Ketal‘s Tyzor® titanate compounds play a critical role in synthesizing high-quality polyolefins via Ziegler-Natta catalysis.
Ziegler-Natta catalysts are heterogeneous systems used in the polymerization of α-olefins. Titanium-based compounds such as Tyzor® serve as the active transition metal component in these systems. When combined with organoaluminum co-catalysts (e.g., triethylaluminum), Tyzor® catalysts facilitate the controlled polymerization of ethylene, propylene, and their copolymers into high molecular weight, stereoregular polymers.
One of the key benefits of using Tyzor® as a titanium source in polyolefin catalysis is the precise control over polymer stereochemistry. In polypropylene production, for example, Tyzor®-based catalysts enable high isotacticity—resulting in superior mechanical properties, thermal resistance, and clarity. This makes them ideal for producing homopolymers, impact copolymers, and random copolymers with tailored performance for packaging, textiles, and automotive interiors.
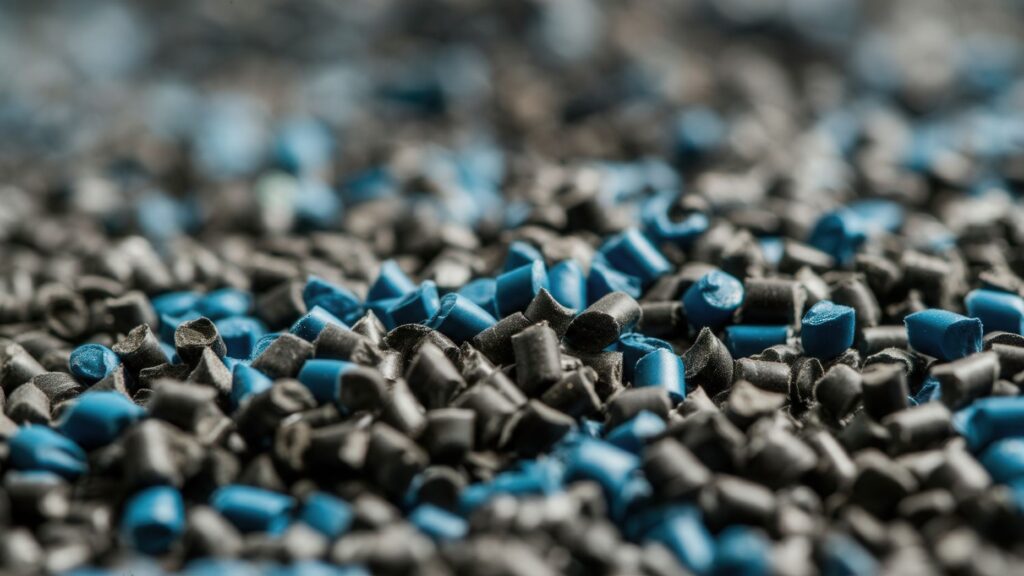
Enhancing Polyolefin Efficiency and Performance
Enhancing Polyolefin Efficiency and Performance
Another key advantage of Tyzor® titanates is their ability to produce stereospecific, narrow molecular weight distribution polymers with consistent morphology. This translates into improved extrusion behavior, better impact resistance, and excellent processability for film, fiber, and molded part applications.
From an environmental standpoint, Tyzor® catalysts are part of the move toward non-phthalate-based catalyst systems that meet global regulatory and consumer safety expectations. These systems support the production of medical-grade and food-contact polyolefins without compromising catalytic activity or product quality. Furthermore, Tyzor® compounds can also be utilized in the development of dual-supported or metallocene-enhanced systems, where traditional Ziegler-Natta platforms are augmented to achieve novel polymer architectures and advanced functionalities—such as clarity, elasticity, or toughness.
Polyurethane-Polyol Synthesis
Polyols are critical building blocks in formulating polyurethane (PU) systems, influencing everything from flexibility and hardness to chemical resistance and curing behavior. Dorf Ketal‘s Unilink® and Tyzor® catalysts provide advanced solutions for optimizing polyol reactivity and polyurethane performance across diverse applications—including elastomers, coatings, adhesives, and sealants.
Polyols are generally categorized into two types: polyether polyols and polyester polyols. Both can be functionalized with primary or secondary hydroxyl groups, which dictate their reactivity with isocyanates. Primary polyols (–OH attached to a terminal carbon) exhibit higher reactivity, making them preferred substrates for high-performance applications. However, secondary polyols are often favored for certain properties like hydrolysis resistance, though their reactivity is up to 70% lower.
Dorf Ketal‘s Unilink® series catalysts are specifically engineered to address these challenges. Products such as Unilink® 1030 and 1020 offer fast reactivity akin to tin-based systems and are especially effective in water-free polyester-based systems used in cast elastomers. These catalysts enable a consistent and controlled reaction profile with aliphatic and aromatic isocyanates, allowing formulators to meet tight processing and curing specifications.
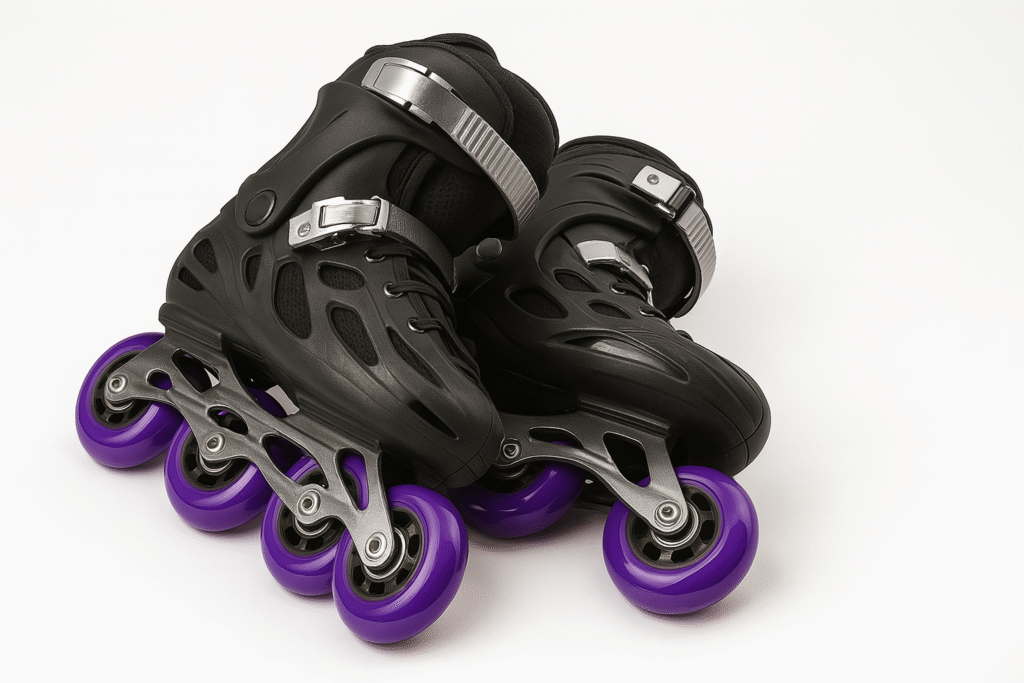
Smart Reactivity for Polyurethane - Polyol Synthesis
Smart Reactivity for Polyurethane - Polyol Synthesis
In systems where water stability and long pot life are required—such as two-component PU coatings and adhesives—Unilink® 2130, 2200, and 2500 series provide delayed curing profiles that mimic the behavior of mercury catalysts. These catalysts are designed for compatibility with both polyether and polyester polyols and allow formulators to tailor Shore A hardness across a wide spectrum of PU systems. This is especially valuable for elastomeric applications where a balance between flexibility and durability is crucial.
Unilink® catalysts also enhance polyol compatibility by minimizing premature side reactions, improving storage stability in the polyol component. This translates into greater formulation robustness and extended shelf life—key concerns in industrial-scale PU manufacturing. From an environmental perspective, Dorf Ketal‘s catalyst technologies help reduce reliance on hazardous materials such as organotin and mercury. As global regulatory pressures increase, especially in automotive and building materials, Unilink® catalysts offer a viable path to compliance without sacrificing performance.
Tyzor® catalysts also support polyol-based systems by promoting crosslinking in water-based and solvent-based adhesives and coatings. These organotitanates can react with hydroxyl-functional resins to create tougher, more chemically resistant networks, making them suitable for hybrid PU/acrylic systems and moisture-cure sealants.
Recommended Products
Subcategory/Type
|
Primary Products
|
---|---|
PBT, PPT, Others
|
Tyzor D-140, Tyzor TnBT, Tyzor TPT, Tyzor TPT-20B, ACtivate 422, ACtivate 436
|
Polyolefin
|
Tyzor D-140, Tyzor NPT, Tyzor TnBT, Tyzor TPT, Tyzor TPT-20B, Tyzor ZT-120
|
Polycarbonate
|
Tyzor TnBT, Tyzor TPT, Tyzor TPT-20B
|
PET
|
Tyzor 64, ACtivate 422, ACtivate 436
|
Polyol/Polyester
|
Tyzor TE, Tyzor 9000, Tyzor TnBT
|